At Micronair we have a real depth of experience in the equipment used by Timber processors and in today’s Joinery Workshops. And we have a range of extremely well proven solutions to saw dust and shaving problems in these environments.
Sawdust collection system. Dust extraction woodworking. Dust collections systems woodworking
Today Moulders are operating at ever faster speeds, producing higher quantities of shavings - and often you are machining some panel based product or otherwise producing finer dust filtration requirements.Tougher EPA requirements mean traditional cyclones cannot meet today’s demands. Machine manufactures now specify significantly higher airflow and pressure minimums than earlier generation machinery requirements also - so the Extraction and filtration task is tougher.
Our VIBRA-CLEAN and CLEAN-FLOW models are all well suited to these applications as they have 'clean air' high pressure fans up to 55kw as standard and larger on request - so whatever plant size and layout you have - we will custom design a perfectly matched solution.
We offer a variety of filter media and designs and a choice of automatic and economical Vibration cleaning. With VIBRA-CLEAN this takes place at workshop shut-downs through whereas our super efficient continuous auto cleaning via reverse pulse utilising our ULTRA-FLOW technique is the ideal solution when volumes are larger.All cleaning is done without removing the filters - clean, convenient and fast!
All systems are 'negative pressure' and this is a huge advantage in retaining fine dust. Essentially the entire system is operating at a pressure below the outside atmosphere pressure - which means even if there were a 'leak point' it would draw air into the system there - not leak dust out.
Sawdust and waste can be collected in bins under the Extractor - or where large daily volumes are present - waste can be conveyed to large 'over truck' hoppers for similar for easy loading and transport off site.
We can also custom design an efficient ductwork layout using our in-house design software that carefully matches airflow and pressure specifications of your individual machinery and its utilisation % against pressure friction losses and air/filter ratios to determine the right combination of extractor model and fan / motor are specified. This is a very important step to ensuring your system is matched and balanced and works to the highest level of efficiency
Efficiency is further enhanced via clever Variable speed Drive control and auto shut off gate options that work together to maximise system efficiency and deliver huge energy savings year after year.
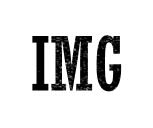